Choosing the right maintenance provider is a critical decision for any commercial vehicle operator in the UK. The quality of maintenance directly impacts vehicle safety, compliance, and operational efficiency. Here’s a comprehensive look at the key criteria for selecting a professional maintenance provider.
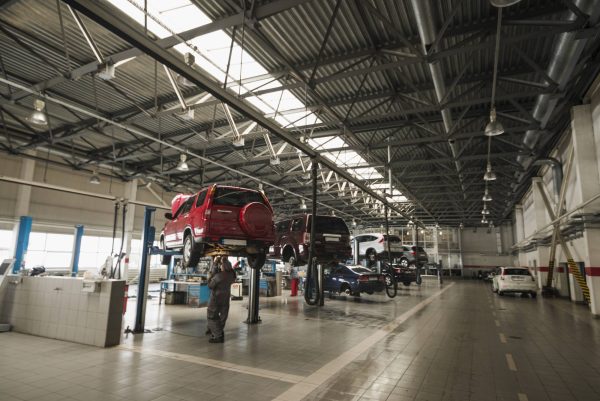
Workshop Accreditation and Standards
One of the most important factors to consider is whether the maintenance facility has achieved recognised quality standards. Look for providers that have manufacturers’ franchised workshop quality standards or independent assessments, such as the IRTE National Workshop Accreditation Scheme. The new Maintenance Provision Rating Scheme (MPRS), being trialled in 2024/25, will provide an additional benchmark for workshop quality.
Technical Competence and Training
The technical competence of maintenance staff is paramount. Service inspectors should ideally hold relevant technical qualifications and achieve automotive technical accreditation such as IRTEC. For modern vehicles with complex systems, ensure the provider has specific training for alternative-fuelled vehicles and Advanced Driver Assistance Systems (ADAS).
Facilities and Equipment
The maintenance provider must have adequate facilities for your fleet size and vehicle types. Essential equipment should include:
- Undercover accommodation suitable for your largest vehicles
- Appropriate lifting or inspection facilities
- Brake testing equipment
- Emissions testing capability
- Headlamp alignment equipment
- Access to diagnostic equipment
Quality Control Systems
Look for providers with robust quality control systems in place. This should include documented procedures for inspection, repair, and sign-off processes. The provider should be able to demonstrate how they monitor and maintain standards, including regular audits and staff training programs.
Contract Management
A clear, written contract is essential. This should detail:
- Precise scope of vehicles covered
- Inspection frequencies
- Type of checks to be performed
- Repair policies
- Any subcontractor arrangements
The provider should also be willing to share performance data such as MOT first-time pass rates and completed inspection documentation.
Communication and Accessibility
Effective communication is crucial. The provider should have systems in place to:
- Provide timely access to inspection records
- Alert you to serious defects
- Offer technical advice when needed
- Respond promptly to urgent maintenance needs
- Provide clear documentation of all work performed
Consider their geographical location and operating hours to ensure they can meet your operational needs.
Cost Considerations
While cost is important, it shouldn’t be the primary factor. Consider the total cost of ownership rather than just the hourly rate. A cheaper provider might prove more expensive if they provide poor-quality work that leads to vehicle downtime or compliance issues.
Track Record and References
Research the provider’s reputation and experience in maintaining similar vehicles to yours. Ask for references from existing customers, particularly those operating similar fleets. Check their history with relevant industry bodies and their standing with the Traffic Commissioners.
By carefully evaluating potential maintenance providers against these criteria, operators can make an informed decision that supports their compliance obligations and operational needs. Remember that the responsibility for vehicle roadworthiness ultimately remains with the operator, making this selection process crucial for maintaining a safe and compliant fleet.